As a safety or operations manager, part of your responsibility is to assess the available safety solutions to determine the best fit for your organization. Reviewing the various features and benefits can be challenging enough, but when it comes to the bottom line, evaluating the return on investment (ROI) of safety solutions can feel a bit uncomfortable. How do you put a price on workers’ health and keeping them safe?
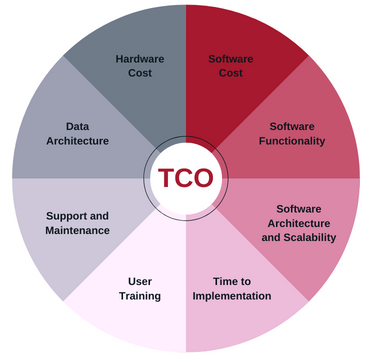
The human cost of not having the right safety solution at the right time is a cost we all want to avoid – it’s why we do what we do! It goes without saying that avoiding the operational and lost productivity costs associated with safety incidents are also important when evaluating safety solutions.
But there are additional factors to consider when determining the total cost of ownership (TCO) of potential safety solutions. These can be roughly categorized into the “hard” costs of the devices and consumables, and the “soft” costs of implementation, training, maintenance and operations.
Here we take a holistic view on the factors that contribute to TCO and how connected safety solutions can provide savings, that ultimately affect your ROI.
How connected gas detection and safety saves on hard costs
When looking at the hard costs of personal safety devices, simply tallying the purchase, lease or rental price of the detectors along with the maintenance equipment, such as those required for bump testing and calibration, misses some critical factors that play into overall TCO. Other factors to consider include time savings from increased device functionality, overall lifespan and reducing sunk costs from lost devices.
Industry workers face a variety of safety hazards every day, whether at facilities, or working remotely and travelling between worksites. You could look at every location, application or task to determine the best solution for each or find a flexible and comprehensive solution that covers the spectrum of requirements to protect your workers from the various hazards they may encounter.
READ MORE:
Top 4 Ways Connected Safety Prevents Incidents For Your Water and Wastewater Workers
How Connected Safety Proactively Reduces Risk to Oil and Gas Facilities and Workers
Blackline’s G7 personal wearables combine gas detection, lone worker safety, communications through push to talk and text (PTT – like a walkie talkie) and location tracking. The G7 can also be configured to detect one or multiple gases by simply swapping out the cartridge on the same device. If a worker needs to detect for only H2S one day, Cl2 the next and then multiple-gases the following day, they can carry one device and various cartridges with different sensor configurations for plug-and-play flexibility that reduces redundancy and training, and increases worker productivity.
As an added bonus, using devices with location monitoring allows workers to find their device if they left it in the lunchroom, vehicle or if it fell off while working – getting them back on the job fast. By mitigating lost devices combined with a longer lifespan, investing in Blackline’s G7 personal wearables also means you’ll reduce the need for extra inventory.
How connected safety saves on soft costs
Much like the hard costs of safety solutions, there are hidden soft costs that if considered in your TCO analysis can reveal some serious upside. Connected safety solutions streamline operational churn by reducing device maintenance and false alarms, saving IT resources’ time and streamlining evacuations and drills.
Reduce Maintenance Costs
Looking at maintenance, gas detection devices need to be kept in compliance through regular bump testing and calibration. This often falls to third-party service providers, not only incurring costs but taking the devices out of service. Blackline’s G7 single- and multi-gas detectors use a fast and simple docking system that costs less than competitors and empowers individual workers to bump test and calibrate their devices. There’s no need to bring in a third-party to keep devices compliant and no additional IT infrastructure required. You can also confirm the status of all devices via the online portal, dashboards and reports to ensure workers are fulfilling the requirement to keep their device compliant.
Reduce False Alarms
False alarms can be relatively frequent with conventional safety devices resulting in costly and unnecessary evacuations. This can lead to workers becoming complacent, even ignoring or turning their devices off so they can just get the job done, increasing the risk of safety incidents. As with compliance and calibration, using a connected safety solution means all device readings are available in real-time so they become more trustworthy rather than an annoyance. You also don’t need to wait for the devices to be docked to download critical information – adding efficiencies that save time, and costs.
Eliminate IT Set-up Requirements
At first glance, you may think that using connected safety would require a draw on IT, but the opposite is true. Setting up and maintaining IT infrastructure, such as mesh networks, takes resources and time, translating into indirect soft costs that affect TCO of your safety program. Using cloud-connected devices negates all these costs and enables automatic, over-the-air (OTA) settings and configuration, removing the need to dock the devices for firmware updates.
Improve Evacuation Management Process
Because worker location is provided in real-time via an online portal, connected devices eliminate the need for manual headcounts and increase worker safety. Instead of having to send out search parties, worker locations are known, and rescuers can go directly to where help is needed. This not only saves precious time in an emergency evacuation but greatly reduces drill times, allowing workers to return to the task at hand – increasing productivity.
READ MORE:
Leave No One Behind: How connected safety technology streamlines evacuation management
Conclusion
Using a flexible, comprehensive connected safety solution mitigates the need for multiple devices and extra inventory, reduces IT resources and operational churn, and cuts down on training and change management – all lowering the TCO of your safety program.
We hope this review of the hard and soft costs that contribute to the overall TCO has been helpful as you evaluate options for your gas detection and lone worker safety needs.
Have more questions?
Don’t hesitate to contact our team of experts.
Learn more:
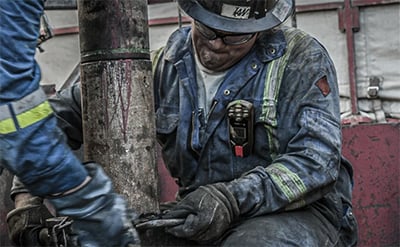
|
|
Protecting Gulf Coast Oil and Gas Workers Learn more about the specific hazards oil and gas workers face in the Gulf Coast/ PADD 3 region, including additional articles, eBooks and white papers.
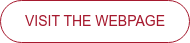
|