Every industry is seeing the effects of digital transformation and the water and wastewater industry is no exception. Automation and digitization of water utilities is becoming a necessity to increase operational efficiency and optimize water resources to sustainably address challenges such as aging infrastructure, decreasing water supply and extreme weather events, to name a few.
Worker safety is a critical area being transformed by the application of digital technology.
Because of the wide range of operations, tasks, and locations, workers in the water and wastewater industry are exposed to a variety of safety risks. When facing multiple hazards becomes part of the day-to-day routine, workers can become complacent – at worst resulting in high-profile workplace fatalities.
|
Tasks
- Confined space entry
- Inspections and cleaning
- Maintenance and repairs
- Water recovery
- Sewage disposal
- Water disinfection, chlorination and dechlorination
|
|
Facilities
- Wastewater treatment plants
- Waste digesters
- Pumping stations
- Sludge-handling facilities
- Chemical-handling facilities
- Sewers
|
Instead of waiting for a “triggering incident” to occur, many water and wastewater municipalities and facilities are taking proactive steps to protect their essential workers using connected safety solutions. This means going from simple “beep-and-flash” gas monitors and manual check-ins to continuous, real-time gas detection and monitoring the status of your workers and facilities – wherever and whenever.
In a nutshell, connected safety solutions combine cellular or satellite connected devices – both wearables and area monitors – with cloud-based software and data analytics to show real-time gas exposure levels, and worker location and safety status (e.g., alert notifications if they’ve fallen). This provides safety managers with continuous situational awareness. The devices also serve as a critical communication lifeline for workers should they need immediate assistance.
Incident detected Fall, no motion, high gas & more |
|
Incident data streamed to the cloud in real-time |
|
Alert data collected in Blackline Live |
|
Monitoring personnel manage the response according to customized response plans |
|
Help is sent directly to the worker’s exact location |
|
|
|
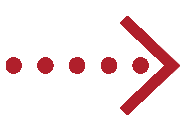
|
|
|
|
|
|
To understand how and where connected safety solutions can proactively prevent incidents, below are the top four ways that continuous, real-time monitoring can make the difference in getting water and wastewater workers home safe.
1) Gas Detection
Typical hazardous gases in water and wastewater applications are methane (CH4), hydrogen sulfide (H2S), chlorine (Cl2), and oxygen (O2) enrichment or depletion. Wastewater plants may also emit sulfur dioxide (SO2), ammonia (NH3), ozone (O3), and chlorine dioxide (ClO2). The risks associated with exposure to harmful gases are magnified by the high temperature and humid conditions of water and wastewater environments.
WATER AND WASTEWATER TREATMENT FACILITIES TYPICALLY MONITORED |
Chlorine (Cl2) |
Carbon Monoxide (CO) |
Hydrogen Sulfide (H2S) |
Lower Explosive Limit (LEL) |
Ammonia (NH3) |
Oxygen (O2) |
Sulfur Dioxide (SO2) |
Water Collection (Dams, reservoirs, lakes, rivers, collection and storage tanks) |
✓ |
✓ |
✓ |
✓ |
|
|
|
Storm and Wastewater Collection (Dry/wet wells, manholes, sumps, treatment plants) |
|
✓ |
✓ |
✓ |
|
✓ |
|
Water Treatment (Treatment areas, chemical storage tanks, injection stations) |
✓ |
|
|
|
|
✓ |
|
Wastewater Treatment (Gas treatment and storage areas, digester, sediment, holding, aeration and clarification tanks) |
|
|
✓ |
✓ |
✓ |
✓ |
✓ |
Water Transmission and Distribution (Meter pits, vaults, pipelines, trenches) |
✓ |
✓ |
✓ |
✓ |
|
✓ |
|
Plant Operations |
✓ |
|
✓ |
|
|
|
|
The integrated location tracking capabilities of the Blackline G7 personal gas detector means that if a worker is exposed to hazardous air quality, supervisors are alerted in real-time as to their precise location and the gas levels encountered in the area. This results in quick response times and safer ones since the response teams know the situation before a rescue operation is started (e.g., whether gas levels indicate SCBA is required).
The sheer variety of gases that workers may be exposed to through their day-to-day activities makes the customizable multi-gas sensor cartridges ideal. They can simultaneously detect up to 5 different gases and are easy to swap out, so one device can do the job of many. The cartridges can even be changed on the job or while in transit to a new incident or worksite where it is known there is risk of a particular gas.
2) Confined Space Entry
The Occupational Health and Safety Administration (OSHA) definition of a confined space has three components:
- It must be large enough for workers to enter and perform certain jobs
- It must have limited means of ingress/egress
- It must not be designed for continuous occupancy to work in the space
There are several types of confined spaces encountered in the water and wastewater industry, including treatment units, tanks and reservoirs, water towers, sewers, sumps and manholes. These environments present serious risks to workers, not only from exposure to increased concentrations of toxic gases or oxygen depletion, but also due to falls, fire and explosions, and extreme temperatures.
Confined space entry is a leading cause of occupational fatalities in the United States and are increasing year over year.
According to the US Bureau of Labor Statistics, between 2011 and 2018 there were 27 fatalities from inhalation of a harmful substance in sewers, manholes, and storm drains. With 16 fatal incidents, these confined space wastewater locations were also one of the most common areas for falls with seven more occurring in septic and water tanks.
Because confined spaces can have consistently high levels of gas, individual beep-and-flash units are ineffective, and workers are prone to turning them off. To ensure safe working conditions, confined spaces require both pre-entry and continuous gas monitoring. Blackline’s wearable G7 Multi-Gas Pump detector's pre-entry mode can be used to sample the air quality of a confined space before access and then put into diffusion mode to continuously monitor the space as workers complete the job.
Alternatively, if confined space access is required over a longer period or when there aren’t workers actively present, Blackline’s G7 EXO area monitor’s long battery life allows for continual access without the need to re-permit.
3) Lone and Remote Workers
When it comes to connected safety, one of the most impactful applications is to protect lone and remote workers. Water and wastewater responsibilities often require working and travelling alone during the day and around the clock – like checking water quality at remote pumping stations or reservoirs. Workers can experience a slip, trip or fall, a health condition, or even an extreme weather event, that can become serious without a quick, easy way to call for help.
Blackline Safety’s cloud-connected wearable devices have an emergency SOS latch alongside two-way voice or text communication, reassuring workers that they have a lifeline linking them to immediate help. Additionally, supervisors can inform workers of weather events or other vital information.
Check-ins can be streamlined using an automated, pre-configured countdown timer. With a push of a button, the worker can acknowledge that they are OK without relying on email or calls. If a check-in is missed and the worker fails to respond to an alert, the device can even trigger an emergency response.
The Encina Wastewater Authority (EWA) recognized this challenge and committed to monitoring their lone workers with Blackline solutions.
“Blackline Safety lone worker devices are so much easier and effective than manual call-in systems. Remote supervisors all feel confident that the safety of our employees is in good hands. Blackline serves our unique needs for safety in the wastewater industry.”
– Jean Tobin, Safety & Training Manager, EWA
4) Facility Safety
Employees not being in constant, direct contact with co-workers can also occur in facilities such as multi-floor pump stations where tasks put workers beyond sight and sound. Blackline’s all-in-one personal gas detection, location and communication devices provide the same proactive protection to your facility staff as lone and remote workers.
Connected safety monitoring devices can also send gas detection data that is below alarm levels. This helps facilities identify potential hazards before they become an incident and proactively repair the issue before it results in worker injury.
Additionally, area gas monitors can be placed in a perimeter around a facility to confirm the levels of gases which may cause odor issues and complaints. This helps create trust with neighboring communities that your facilities are well-monitored and operated safely.
Because all these devices connect directly to Blackline Live, there’s no limit on the number of devices in your network – so you can see the real-time safety status of every unit in your operation.