From food production to automotive fabrication, the manufacturing industry incorporates a diverse spectrum of manufacturers, including biotech and pharma.
Engineers, operators, assemblers and compounders face the dangers of working with and near heavy machinery, conveyor belts, combustible liquids and spray booths. Warehouses and production plants are noisy and fast-paced, with many moving parts.
INDUSTRY STATS
According to the Bureau of Labor Statistics in the United States, this industry reports more than 300 work-related fatalities each year. About 12 million people are employed in the industry, with nearly 400,000 non-fatal injuries reported annually.
Health and Safety Executive (HSE) in the United Kingdom reports that in 2013 and 2014, manufacturing accounted for about 10 percent of fatalities in the British workforce, with nearly one in five reporting non-fatal injuries.
A lucrative sector, the National Association of Manufacturers reports that “for every $1 spent in manufacturing, another $1.40 is added to the economy. That is the highest multiplier effect of any economic sector.”
In Canada, the manufacturing industry achieved similar results and according to an analytical paper from Statistics Canada, “manufacturing sales reached an all time high in 2014, increasing 5.3% to $621.7 billion.”
Because the manufacturing industry is so important to economies globally, here we explore eight safety incidents you shouldn’t overlook.
1. HANDLING MATERIALS
Manufacturing workers are responsible for moving materials in raw, in-process and ready-for-market states. Inappropriate handling of the materials can be very risky, resulting in overexertion and exhaustion, risk of equipment failure and complacency that may lead to procedures followed incorrectly. Employees who don’t value the importance of physically lifting objects the right way risk strains and sprains and even broken bones. Heavy equipment such as forklifts, scissor lifts present numerous dangers to personnel.
2. LOCKOUT/TAGOUT
Making sure safeguards are in place when maintaining equipment should be a top priority for employers. Personnel—often lone workers—can succumb to injuries, especially when working around machinery. In an environment with many moving parts and electrical hazards, it is essential to implement a lockout/tagout procedure to confirm the power has been completely disconnected and cannot be turned back on while an employee is working on the equipment.
3. FATIGUE
Your employees are familiar with working long shifts in fast-paced environments where fatigue is a common contributor of workplace incidents. Mitigating exhaustion with regular breaks, processes and procedures can reduce the risk of employees suffering from fatigue.
4. COMPLACENCY
Working in a high-risk, high-paced calls for motivated and attentive personnel. Heavy machinery, forklifts and moving vehicles can be dangerous. Mistakes and carelessness can lead to injuries and even fatalities. Clear safety measures, regular communication, keeping safety top-of-mind and the right PPE can help alleviate this risk.
5. INCONSISTENT MAINTENANCE
When equipment is not properly maintained, the work environment can be extremely dangerous. Not to mention the risk of malfunctions. On-site workers should be prepared and know what to look for when a machine is malfunctioning. Employees should be on the lookout for warning signs like alarms, vibrations, leaks, unfamiliar noises and exposed wires or smoke.
6. TRAINING
Many organizations believe they have the appropriate training in place for their employees. Does your training following best practices? Does it cover all the ins and outs of manufacturing, including machinery and handling materials?
Working with dangerous equipment and moving objects can be challenging. While many of your team know how to use their equipment, can you ensure their colleagues know what to watch out for when working around the equipment?
7. TIME
Does your business have an emergency response protocol? Has it been updated lately and how is it triggered? If an incident occurred with an employee working alone right now, how quickly could a responder be on-site to help? Are you still using a check-in process and have not made the jump to safety monitoring technology? Do you have a work-alone policy?
Knowing that the unexpected can occur, and should it become a reality that your team faces, you need to be assured that organization has implemented the policies and processes required to keep your team safe. You must be prepared—at all times—to manage the most rapid emergency response possible.
8. THE RIGHT SOLUTION
Your program must be seamless, clear, concise, communicated and measured. If an injury, health incident or assault occurs, your safety monitoring program must efficiently pinpoint your crew members’ precise location.
Do you have the right procedures in place to send an emergency response to your team when an incident occurs? Find out now. Let’s talk about how we can help elevate your current safety monitoring program, connect with us today.
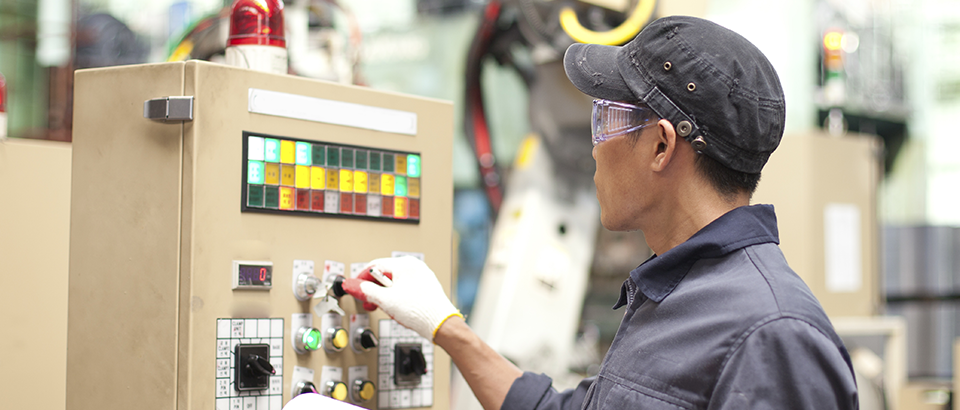