But what’s the best way to go about safeguarding your lone workers — and your bottom line? Here are three critical steps to deliver the results you’re looking for.
Prevention begins with understanding and identifying all the ways employees can be harmed
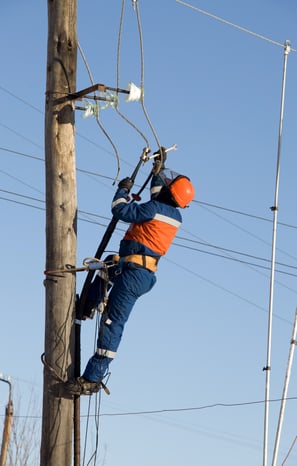
A risk assessment for lone workers starts by identifying each type of lone worker situation in your workplace and then assembling carefully curated teams to meticulously analyze them. Teams should consist of members with differing skill sets to create a committee able to fully assess a situation—and its potential risks. Someone with health and safety expertise could, for example, get paired up with someone with chemical assessment experience, along with a person with in-depth knowledge about the equipment used.
Step-by-step analyses on workplace activities (daily ones, as well as those that may happen monthly or quarterly) should be completed to flag situations that can cause injuries or threaten health. These might include substances used that may be potentially harmful; risk factors associated with the equipment used; and the identification of times when a lone worker is particularly at risk. Some risks may be inherent in all lone worker jobs, while others may be specific to certain geographies and roles.
Some ways to do this to help inform your analysis are:
- Review manufacturer’s data sheets and instructions for each piece of equipment and chemical used and identify pertinent safety information.
- Consider implications of long-term exposure to chemicals, noise, and other hazards.
- Factor in weather-related hazards such as extreme hot or cold temperatures. In frigid weather, frostbite and other dangers can occur. Conversely, when temperatures skyrocket, workers can suffer from fatigue, dizziness, headaches, and muscle cramping; can become dehydrated; and even faint. If any of these happen when a worker is operating equipment or working from heights this can be exceptionally dangerous, and potentially fatal.
- Review and look for patterns in your company’s accident and ill-health records.
- Seek input on procedures — from employees as well as from a designated person who isn’t familiar with your work sites — to gather different perspectives.
- Observe workers during different days and on different shifts without interruption. Record your observations.
- Establish focus groups to discuss risks and possible solutions.
This lone worker risk assessment checklist can help support this process.
Step Two: Create a Plan to Mitigate Risk
Categorize risks—then eliminate, reduce or manage them
Once the risk assessment has been completed with the potential risks for each group of lone workers identified, the next step is to evaluate how your company is currently addressing these risks and to fill in the gaps, as appropriate, to mitigate risk even further. This should entail categorizing them according to if the risk can:
- Be entirely removed
- Be reduced, for example by changing procedures, improving training, adding staff, using scaffolding or by other means.
Finally, determine what procedures you’ll need to implement to mitigate the risks that remain—or any new risks that may be created as a result of changes. Hazardous areas, for example, may be shut off unless a worker absolutely must be there. Protective gear can be improved upon, first aid stations added, and communication devices can be enhanced to keep lone workers safely connected.
Step Three: Invest in Lone Worker Safety Devices and Monitoring
Beyond saving lives, profitability and morale are boosted over the longer-term
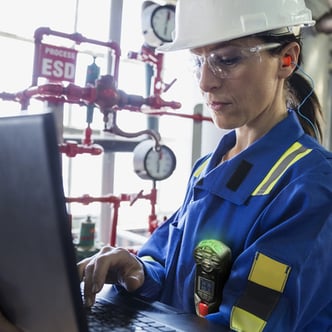
What to look for in lone worker safety devices
Devices that offer integrated solutions for lone worker safety are your best bet; avoid “one-trick ponies.” It’s clunky and less practical to find a different device for each individual monitoring and safety function required—and then you may find that these individually acquired devices don’t work well together.
Ensure that the devices have highly effective connectivity, avoiding ones that simply rely upon a worker’s cellular coverage. The goal is to have a highly reliable lifeline for each and every employee, using modern technology. Both cellular and satellite are an ideal combination to ensure a worker is connected in even the most remote locations.
What to look for in lone worker monitoring
When an incident occurs, your company must respond in real time and every detail counts. It’s crucial to understand:
- Who is involved
- What happened
- Where the employee is located, precisely, whether indoors or out
- Whether other coworkers are nearby
- If the threat is an ongoing one
Nobody has time to constantly monitor a map of worker locations, which is why investing in a monitoring solutions with customizable alerts is a good bet. Alerts should include the worker’s name, location, and reason for the alert – whether it’s a person-down alarm, panic situation, missed check-in or exposure to a gas hazard. Alerts can be employee-activated if the worker is conscious, but the technology should also have the capability to send an alarm automatically if no motions is detected. Remote monitoring teams should be available 24/7 and trained to respond to any type of emergency when it arises.
Boosting morale and bottom line
In a recent Lockheed Martin Corporation case study, they found that developing a safety culture resulted in increased employee productivity +24% and reduced costs by 20% (Source).
“Establishing a safety and health program to prevent occupational injuries and illnesses is not only the right thing to do, it’s the profitable thing to do. Studies have shown a $4 to $6 return for every dollar invested in safety and health.”
– Occupational Safety and Health Administration (OSHA)
The reason? Workplace incidents and fatalities are expensive. A workplace fatality, for examples, averages $1.4 million in direct costs, with an additional $2.1 million in indirect costs per incident (Safety and Health Magazine).
All of this is extraordinarily expensive, dollar-wise, and takes an even greater toll on people. According to the American Society of Safety Engineers, “Anyone who has had the misfortune of witnessing or handling the aftermath of a serious or fatal on-the-job injury knows that, without question, the costs go far beyond those that appear in a company’s ledger book. For those who survive, or who work with the accident or illness victim, the costs will continue with psychological stress that may require years of counseling.”
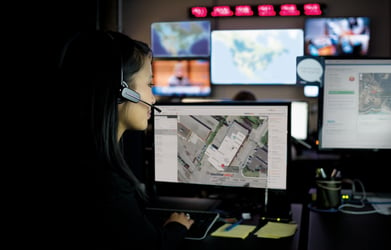
Workers that know their wellbeing is monitored 24/7 by safety professionals who can respond instantly should an incident occur, reduces workplace stress and increases morale and productivity.
Investing in monitoring also provides assurance to regulatory bodies that you have the proper safety measures in place and less ongoing risk of having an accident or injury occur, leading to reduced insurance costs, and lesser chance of hefty fines from workplace tragedies that may have otherwise been prevented.
The intangible costs – like goodwill or reduce employee turnover —are also significant. Workplaces that provide best-in-class safety protection demonstrate they care about their works leading to enhanced morale, productivity and employee loyalty.
Bring it all Together with Blackline Safety
Wherever there’s a need for safety, we’re there
Blackline Safety is a global connected safety technology leader headquartered in Calgary, Canada and Colchester, UK with offices in Houston, USA and Lille, France. Our talented team of designers and engineers combine their drive for innovation with data-driven customer feedback to create, manufacture and manage our award-winning portfolio of gas detectors, area monitors, and lone worker devices in-house. These connected devices, coupled with our safety software, data analytics and reporting, risk mitigation and operational efficiency, allow us to pivot and adapt quickly to changing market needs.
Interested in learning more?
CONTACT US
Did you miss Part 1?: Compromise is Not and Option with Lone Worker Safety
READ PART 1 HERE