Digital transformation has become an imperative for the oil and gas industry, and connected technologies have proven especially valuable for maximizing uptime and revenue. When production is taken offline, getting back up and running quickly, efficiently, and safely is critical to mitigating costs and preventing future unplanned downtime.
Whether downtime is the result of a planned turnaround, shutdown, or an unforeseen outage, these short-term operations face many unique challenges. For example, team leaders need visibility into workplace productivity and safety for both regular employees and contract workers that are less familiar with the facility and standard safety procedures.
A comprehensive digital worksite solution should focus on optimizing both productivity and safety metrics. This will enable sites to increase their operational efficiency, reduce risk, and minimize revenue impact during both turnarounds and shutdowns.
What is a Digital Worksite?
A digital worksite leverages data from connected Internet of Things (IoT) devices throughout the worksite to derive insights that help oil and gas companies understand where productivity losses are occurring across their operations. These insights enable smart decisions based on real-time information to improve productivity, safety, and profitability.
For example, equipping each worker with a connected personal safety monitoring device - like the G7 Series of personal gas monitors from Blackline Safety - provides valuable data to keep personnel safe throughout the entire shutdown or turnaround. These wearable devices not only alert users to the presence of harmful gases but can also be used to identify and locate individuals that may be in danger. This enables staff to work safely and efficiently even if they are a contractor that is unfamiliar with the worksite - ultimately reducing risk and preventing costly accidents during the turndown project.
In addition, connected devices provide data about how and where bottlenecks occur so they can be identified and resolved quickly. This can save hours or days of work required during a turnaround which, in turn, gets assets back online faster — adding potentially millions in revenue that otherwise would have been lost.
A Digital Worksite in Action
In a recent use case, a multinational oil and gas company deployed a digital worksite solution backed by data science to address both safety and productivity concerns for several turnaround projects. The company equipped each worker with a G7 personal safety and gas detection device. These connected devices not only detect hazardous gases and keep workers safe at the job site but also monitor worker activity and mobility via GPS technology.
Each wearable gas detector would collect and send its location-based data to the cloud in real-time, making it easy to visualize on-site worker movement and gain insights into the entire operation via the Blackline Live portal. In addition to being able to respond to bottlenecks as they occurred, the data could also be used for long-term analysis and optimization of future turnaround projects.
For example, in this use case, the company deployed the digital worksite solution for two consecutive turnaround projects to identify problem areas during the first turnaround, establish solutions in-between, and implement and monitor improvements during the second turnaround.
After the first turnaround, the team identified many opportunities to improve productivity by minimizing worker movement across the worksite. Specifically, general site travel caused workers to lose an average of 10% of their workday outside of the expected areas of work. In addition, the team was able to visualize unexpected movement around the site - like trips to pick up tools or long walks to a lunch area - that were taking workers away from productivity zones for up to an additional hour per shift. This not only decreased productivity but also posed additional safety risks since workers were in unexpected areas.
Armed with this information, the management team undertook a series of proactive initiatives across contractor onboarding and training. They also improved signage and distributed maps showing where auxiliary areas were located across sites, such as tool cribs, the lunch area, bathrooms and more. They then implemented these initiatives on the second turnaround and deployed the same digital worksite solution to measure improvement against their previous baseline.
The result: the company recovered 86% of the lost man-hours from the first turnaround, saving an average contractor cost of ~$45/hour per worker. Additionally, schedule certainty was improved, allowing refinery startup to occur four days earlier, recovering more than $1 million in revenue.
What to Look for In a Digital Worksite Solution
1. Fast, Simple Deployment
For short-term, high workforce capacity projects and unexpected shutdowns, speed to deployment is essential to accelerate the time to value. Rapidly connected wearable devices for each worker and drop-and-go portable area monitors are ideal for these applications, but it’s important to choose devices that work out of the box with minimal setup such as the challenges of establishing a reliable mesh network. For example, G7 personal gas detection devices are available with pre-calibrated sensor cartridges that can be easily swapped in and out depending on the site requirements, with no additional configuration required.
In addition, area monitors like the G7 EXO can be set up in any location and instantly connected to the cloud at the push of a button, greatly reducing required work hours to set up a safety ecosystem. In addition, look for a standalone solution that does not require time-consuming and labour-intensive infrastructure changes which typically results in additional burdens on your IT team and subsequent time delays.
2. Devices with Long Battery Life
Safety and monitoring devices should have a long battery life to ensure continuous gas detection monitoring throughout the project to avoid time wasted frequently checking and replacing batteries. In addition, for work in confined spaces, area monitors with long device battery life reduce the need to swap out equipment and pull new permits, so work can be completed faster without compromising safety. Choose devices, like G7 EXO, whose battery life can be measured in weeks or months–not days or hours.
3. Flexibility to Buy, Lease, or Rent Equipment
The flexibility to buy, lease or rent equipment gives added options for Operations Managers, Safety Managers and contractors to acquire devices, as needed, depending on both the short- or long-term requirements. For turnarounds, in particular, the ability to rent equipment only for the duration of the project when the devices are needed is a smart, cost-saving measure.
4. Real-time Visibility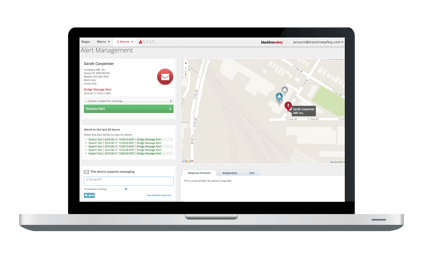
The ability to visualize where workers are, and quickly respond to safety alerts, is key to maintaining high levels of safety. Look for a fully integrated digital worksite solution that instantly aggregates data from each safety and gas detection device in the field for real-time visibility. With an intuitive software interface like Blackline Live, data from the area and personal monitors are immediately visible and clearly displays the exact location and status of each device.
5. Analytics and Insights
The data from connected devices is only as valuable as the insights you are able to derive from them. Robust and intuitive analytics and insights platform should make it easy to visualize key metrics, including worker time spent in productivity zones, heat maps, and transition times (time spent travelling to and from points across the site like toolsheds and lunch areas). For example, understanding how your entire workforce moves throughout the site and determining how many hours are spent in transition gives the opportunity to optimize resource deployment and streamline workflows.
Conclusion
When planning a successful shutdown or turnaround project, safety and productivity go hand in hand. They are both critical to getting back online quickly and minimizing lost revenue due to halts in production. A digital worksite solution that spans both productivity and safety provides the necessary data and insights to make real-time decisions and long-term optimizations that improve operational efficiency.
Bring it all Together with Blackline Safety
Wherever there’s a need for safety, we’re there
Blackline Safety is a global connected safety technology leader headquartered in Calgary, Canada and Colchester, UK with offices in Houston, USA and Lille, France. Our talented team of designers and engineers combine their drive for innovation with data-driven customer feedback to create, manufacture and manage our award-winning portfolio of gas detectors, area monitors, and lone worker devices in-house. These connected devices, coupled with our safety software, data analytics and reporting, risk mitigation and operational efficiency, allow us to pivot and adapt quickly to changing market needs.
Interested in learning more?
CONTACT US
