EMPLOYEE SAFETY IN THE UTILITIES INDUSTRY
Natural gas, electric, water and wastewater utilities pose many risks for your work-alone employees. Electrical engineers and maintenance personnel often work alone for extended periods of time at treatment plants, outdoor pumps and high-voltage substations that can be hazardous. Employees work with machinery, chemicals, toxic gases and other dangers on a daily basis.
Here we explore nine incidents you should not overlook in the utilities industry.
1. ELECTRICAL
According to Electrical Safety Foundation International (ESFI), electrical-related incidents are the No. 1 cause of workplace fatalities in this industry. A study published by the National Safety Council in the United States reports hundreds of workplace fatalities and thousands of injuries occur each year due to electrical hazards alone.
Multiple incidents also occur across water and natural gas sectors, often resulting with workers on disability. Sometimes, these incidents are fatal.
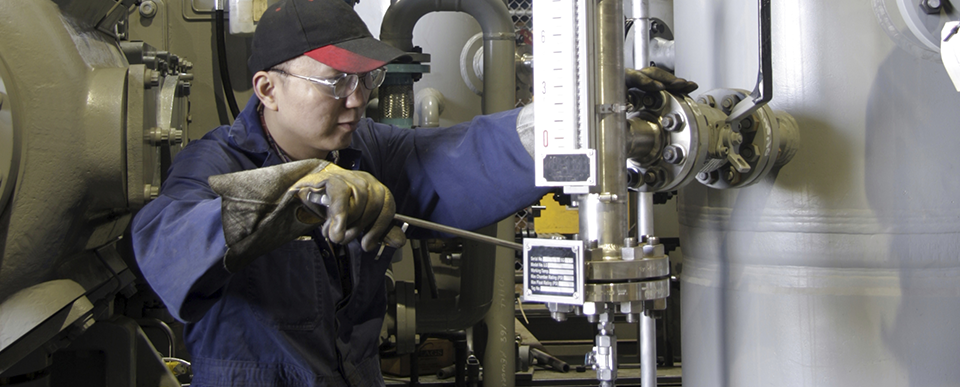
2. TRANSMISSION LINES
More than 110,000 power-line workers are responsible for building and repairing power transmission and distribution systems—they face many risks, according to the Bureau of Labor Statistics
Transmission & Distribution World found that “utility line work is in the top 10 of the most dangerous jobs in America. Around 30 to 50 workers in every 100,000 are killed on the job every year. Many others suffer non-fatal loss of limbs from electrical burns and mechanical trauma. That's more than twice the fatality rate of police officers and firemen.”
3. SLIPS, TRIPS & FALLS
The Canadian Centre of Occupational Health and Safety (CCOHS) reports that more than 42,000 workers are injured annually due to fall accidents.
Meanwhile, the U.S. Department of Labor’s Bureau of Labor Statistics reports 247,120 non-fatal cases involving falls, slips and trips in 2014 and nearly 800 fatalities in 2014, up from previous years.
4. COLD STRESS
The U.S. Occupational Safety & Health Administration (OSHA) warns that “prolonged exposure to freezing or cold temperatures may cause serious health problems such as trench foot, frostbite and hypothermia. In extreme cases, including cold-water immersion, exposure can lead to death.”
“Danger signs include uncontrolled shivering, slurred speech, clumsy movements, fatigue and confused behavior. If these signs are observed, call for emergency help.”
And the Centers for Disease Control and Prevention (CDC) gives this precautionary advice: “Workers who are exposed to extreme cold or work in cold environments may be at risk of cold stress.”
Cold stress can cause a variety of health issues. “Extremely cold or wet weather is a dangerous situation that can cause occupational illness and injuries such as hypothermia, frostbite, trench foot and chilblains.”
5. HEAT STRESS
The Centers for Disease Control and Prevention identifies heat stress symptoms and environments.
“Workers who are exposed to extreme heat or work in hot environments may be at risk of heat stress. Exposure to extreme heat can result in occupational illnesses and injuries. Heat stress can result in heat stroke, heat exhaustion, heat cramps or heat rashes. Heat can also increase the risk of injuries in workers as it may result in sweaty palms, fogged-up safety glasses, and dizziness. Burns may also occur as a result of accidental contact with hot surfaces or steam.”
6. PHYSICAL STRAIN & OVEREXERTION
Your employees are familiar with working long shifts, in fast-paced environments where physical strain, overexertion and fatigue commonly contribute to workplace accidents and injuries. Mitigating exhaustion with regular breaks, mixing up the routine and implementing formal processes and procedures can reduce the risk of employees suffering from fatigue.
Mistakes and carelessness can lead to injuries and even fatalities. Clear safety procedures, regular communication and the right safety equipment can help alleviate this.
7. BIOLOGICAL & CHEMICAL HAZARDS
According to Work Safe Alberta, water and wastewater personnel must be cautious when working with sewage.
“The most serious viral risk is hepatitis and the most serious bacterial risk is tetanus. The main route of exposure is hand-to-mouth
contact,” the agency found. Biological exposure “may occur whenever sewage is agitated, such as near incoming wastewater inlets and sludge treatment areas.”
From a chemical perspective, “sanitary sewers and similar confined spaces containing sewage can sometimes be deficient in oxygen due to organic oxidation and displacement by carbon dioxide. They can also contain flammable gases such as methane and toxic gases such as carbon monoxide and hydrogen sulphide.”
The Health and Safety Executive (HSE) in the United Kingdom warns workers of health risks when working with sewage. “Exposure to sewage or its products may result in a number of illnesses. These include: gastroenteritis, Weil’s disease, hepatitis, occupational asthma, infection of skin or eyes; and/or rarely, allergic alveolitis.”
Employers must ensure their personnel—specifically your lone workers—take the appropriate safety measures when working with sewage.
8. DRIVING
Regardless of where an employee is driving—whether it’s on a long stretch of highway or between sites—drivers of all types of transportation can be challenged by heavy loads, inclement weather, other drivers, bicyclists and pedestrians.
Long shifts and physically challenging duties—like heavy lifting and hazardous working environments—contribute to employee fatigue. The U.S. Department of Transportation reported fatalities rose to nearly 4,000 in 2013, and included truckers, occupants in vehicles that collided with large transport trucks and pedestrians. More than 32,000 highway deaths for all types of vehicles were also reported the same year.
9. EMERGENCY RESPONSE
Does your business have an emergency response protocol? Has it been updated lately and how is it triggered? Are you still using a check-in process and not made the jump to safety monitoring technology? Do you have a work-alone policy?
Should the unexpected can occur, you need to be confident that you’ve implemented the policies and processes required to keep your lone workers safe. Your team must be able—at all times—to manage the most rapid emergency response possible.
Your program must be seamless, clear, concise, communicated and measured. It must ensure that if an injury, health incident or assault occurs, your monitoring program efficiently pinpoints your crewmembers’ precise location—indoors and outdoors— and directs a prompt emergency response.
Do you have the right procedures in place to send an emergency response to your utility and public works personnel when an incident occurs?
Find out now—let’s talk about how we can help elevate your current safety monitoring program. Connect with us today.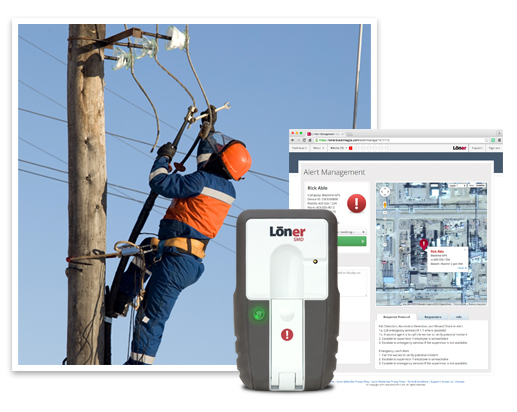